Peugeot was the 2012 European leader with low CO2 figures of 121.5g/km. In 2013 Peugeot has been reducing the weighted average emissions of CO2 of its European range still further and at the end the May this figure stood at 116.3g/km.
New technologies have allowed Peugeot to achieve an ambitious CO2policy target of 95g per kilometre on the weighted average of their new vehicles sold in Europe in 2020, offering particularly economical engines with fuel economy of 141mpg achievable.
BlueHDi refers to the exclusive diesel emission control technology, uniquely combining oxidation catalysis, SCR (Selective Catalytic Reduction) and the Diesel Particulate Filter (DPF) with additive ̶ the only one to combine reduction of NOx by up to 90%, elimination of particulates and reduction of fuel consumption and CO2 emissions.
HYbrid Air combines petrol and compressed air in a full hybrid solution. The simplicity, durability and international nature of this technology make it potentially available to the largest audience of consumers. HYbrid Air is a key step in reaching the target of getting over 140mpg.
Peugeot’s 208 HYbrid FE is another innovative solution to improving fuel economy. This non Plug-in petrol full-hybrid concept explores many new technologies in partnership with Total, to combine driving pleasure and efficiency with low CO2 emissions and excellent fuel economy.
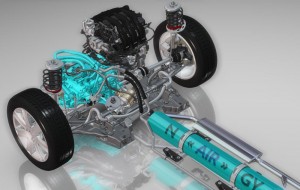
HYbrid Air: a key step towards the heart of the range hybrid
With HYbrid Air technology, PEUGEOT is innovating once more in the interests of the environment and of its customers in all of its markets. In fact, this new drivetrain combines petrol and compressed air to address the growing challenges facing the motor industry.
It is an essential step towards the goal of increasing fuel economy to over 140mpg. To achieve this, it will be combined with the continuous improvement of the engines and the reduction in weight permitted by new platforms.
HYbrid Air, the evidence
The specification for this technology had clear objectives: substantial reduction of fuel consumption and CO2emissions, on all continents, by means of affordable technology, which can be applied to cars and light commercial vehicles of the B and C segments.
To fulfil this specification, HYbrid Air unites tried and tested technologies: harnessing energy through compressed air with a new generation of 3-cylinder petrol engines. Some 80 patents are testament to the expertise mobilised for this important R&D work.
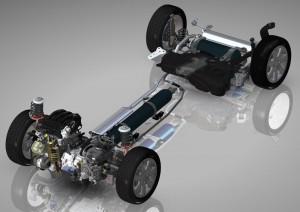
Principle of operation
HYbrid Air combines two energy sources to achieve the best efficiency according to the different situations encountered. Compressed air will assist the petrol engine, or even take its place, to bring the most efficient points of operation during acceleration and moving off. This technology uses certain components which are new to the motor industry, but widely used in other sectors like aeronautics.
HYbrid Air consists of:
- an energy tank, containing pressurised air, installed under the body in the central tunnel,
- a low pressure reservoir at the rear suspension cross member, acting as an expansion bottle,
- a hydraulic unit consisting of a motor and a pump, installed under the bonnet on the driveshaft.
The latter consists of a controlled epicyclic train to manage the distribution between the two energy sources. It replaces the mechanical gearbox and in addition offers automatic gear changes.
The internal combustion engine is the latest generation 3-cylinder petrol engine. It benefits from the most modern technology: optimisation of weight and of the compactness by means of maximising the integration of components, the reduction of internal friction by means of the use of a Diamond-like Carbon coating and Split Cooling thermo-management for a faster increase to operating temperature.
HYbrid Air has the initial advantage of being compatible with the existing platform in the interests of passenger space, modularity and volume of the petrol tank, which remain unchanged.
Three modes: Air (ZEV), Petrol, Combined
The ECU software will control the two sources of energy to achieve the best overall efficiency possible according to the situation. The switch between the three modes available is completely transparent to the driver.
In the Air (ZEV) mode, only the energy contained in the compressed air drives the vehicle. As it decompresses, the air occupies an increasingly large space in the energy tank and so displaces a corresponding volume of oil. This latter is an energy carrier which supplies the hydraulic motor coupled to the epicyclic train. As the internal combustion engine is switched off, the vehicle moves without consuming fuel or emitting CO2. This mode comes into its own when driving in town.
In Petrol mode, only the 1.2-litre VTi 3-cylinder petrol engine powers the vehicle. This engine benefits from the latest technology and results (compared to the previous generation) in a reduction in weight of 21kg, friction is reduced by 30% and thermo-management is modified to reach the optimum operating temperature more quickly. This mode is particularly suited to main roads and motorways at a steady speed.
In the Combined mode, the petrol engine and hydraulic motor operate together to move the vehicle, in proportions adapted according to the situation to achieve optimum fuel economy. HYbrid Air can supply the hydraulic motor from two sources: as long as the quantity of energy in the pressurised air tank is sufficient to fulfil the driver’s requirements, the hydraulic motor operates using this source. Then, if necessary, it can be supplied by the hydraulic pump directly. This mode is intended in particular for moving off and acceleration in town and on main roads.
The energy reservoir is filled in two ways. On deceleration (braking or releasing the accelerator pedal), the vehicle is slowed down not by application of the brakes but by the resistance to the compression of the air in this accumulator. The alternative consists of filling by restarting of the internal combustion engine; in this situation, some of the energy produced by the petrol is used to compress the air. In both cases, the maximum energy capacity of the accumulator under pressure is reached very quickly, in only ten seconds.
On the way to achieving over 140mpg
The flexibility of HYbrid Air offers numerous advantages. By using tried and tested components, its durability makes it perfectly suited to the wide range of driving conditions encountered across the world. This innovative technology has the potential to become the heart of the PEUGEOT range and an international hybrid.
Customers of cars and light commercial vehicles of the small and medium segments will experience:
- Urban driving in Air (ZEV) mode up to 80% of the time, therefore with zero fuel consumption,
- a 45% reduction in fuel consumption when driving in town,
- smooth driving due to the automation of the transmission,
- passenger space and modularity which remain unchanged, as does the capacity of the fuel tank,
- peace of mind due to tried and tested components.
On the current generation of B segment vehicles, HYbrid Air considerably reduces fuel consumption and CO2emissions. In fact, on completion of the homologation drive cycle test, the figures are set at just 97.4mpg and CO2 at 69g/km. HYbrid Air is a key step towards achieving in excess of 140mpg in combination with other technological advances.
An innovative R&D model
Such an ingenious idea cannot just be the result of a conventional development plan. HYbrid Air technology is the end product of a project which mobilised 200 people on the same platform. The expertise represented, from the development of a drivetrain to the strategic vision, by way of customer surveys, worked in very close collaboration with strategic suppliers, which included Bosch.
Finally, HYbrid Air was developed in financial partnership with the ‘Investing in the Future Programme of the Ademe’, the French Environment and Energy Management Agency.
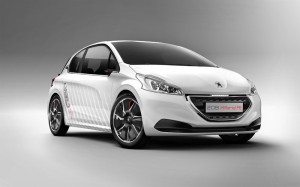
208 HYbrid FE: technology to achieve in excess of 140mpg
In partnership with Total, this non Plug-in, petrol full-hybrid is part of marque’s hybrid strategy.
HYbrid4, the diesel-electric hybrid, has already won over 28,000 customers in Europe with its high-level performance. 208 HYbrid FE explores technological solutions and takes the results even further to achieve record fuel economy using: aerodynamic properties, weight reduction, power train and hybridisation.
A historic partnership
Since 1995, PEUGEOT and Total have been working together to significantly reduce fuel consumption, CO2emissions and TCO (Total Cost of Ownership) of vehicles.
First shown at the Geneva Motor Show 2013, the aim of the 208 HYbrid FE is to combine real driving pleasure with low CO2 emissions. More precisely, the intention is to halve the CO2 emissions of the cleanest 208, equipped with a 1.0-litre VTi 68bhp yet to provide it with the acceleration of a performance hatchback, like the 208 GTi. A real challenge!
Numerous innovations are implemented in several areas:
- Aerodynamic properties: gain of 25%,
- Weight reduction: 20%,
- Power train: 10% reduction in consumption,
- Hybridisation: recovery of 20% of the energy over one cycle.
Aerodynamic properties: gain of 25%
The aerodynamics experts took the Peugeot design and pushed it to the extreme. The Cd is improved by 25%, to a value slightly lower than 0.25, while keeping the passenger and boot compartments unchanged. This performance is achieved in particular by means of components which can be seen from the outside: flat underside, rear diffuser, rear tracks narrowed by 40mm, mirrors eliminated and Tall & Narrow tyres. The size of the radiator grille is also reduced by 40% by means of the progress made on the drivetrain.
Weight reduction: 20%
The 208 HYbrid FE benefits from the expertise of the Polymers Division of the Refining-Chemicals branch of Total, as well as of its two subsidiaries CCP Composites and Hutchinson, in the field of composite materials. These are used extensively to reduce weight by 200kg: with a one-piece shell, under-floor panel, doors, lower front panel, bonnet and wings. They are also used in the passenger compartment: door trim pads, centre console and vent trims.
The Pseudo MacPherson suspension innovates with a composite blade fitted in a transverse position, which replaces several parts: suspension springs, lower wishbones and an anti-roll bar.
Power train, consumption reduced by 10%
The latest generation 3-cylinder engine evolves in combination with a battery and an electric motor taken from PEUGEOT Sport’s Endurance programme.
The efficiency of the petrol engine (68bhp – 50kW) uses the volume of fuel made available to its full potential. The Miller Cycle is optimised and the compression ratio changed to 16:1. Friction losses are reduced by 40% thanks to special reciprocating gears: surface coating, design, balance. The 1.2-litre VTi-FE engine is also modified as regards cooling, towards a minimum of thermal inertia: light engine, less than a quarter of the previous volume and flow of coolant.
The greasing of the EGC (Electronic Gearbox Controlled) manual gearbox, which is standard, is redesigned to reduce the volume of lubricant and prevent splashing of the gears, which consumes energy.
Total Lubricants has developed a prototype oil, offering a friction reduction of 3%, as well as greases for the driveshafts and their homokinetic seals. The high performance oil, of grade 0W12, develops its properties very rapidly with a shorter temperature rise time. Optimised as regards friction, it retains, both when hot and when cold, an advantage compared to the best products on the market.
Hybridisation, 20% of the energy recovered over one cycle
The gearbox design is specific with the electric motor fixed to the differential crown wheel. The arrangement permits the provision of reverse gear, by inverting the direction of rotation and of the starter function while also providing purely electric ZEV (Zero Emissions Vehicle) driving. The electric motor combines power and lightness (only 7kg), it develops 30kW as a motor and 100kW as a brake.
During the deceleration phases, whether this is on releasing the accelerator pedal or on braking, the vehicle is slowed down preferentially by the electric motor. The hydraulic circuit only comes into operation at the end of braking. During this phase, the electric motor operates as a receiver to recover the energy and charge the Lithium-ion battery. Then, on acceleration, this energy is returned and assists the petrol engine.
Source; Peugeot